Lidar: Application in rail transit
LiDAR (Light Detection and Ranging) technology, as an active remote sensing technique, acquires precise 3D spatial information of target objects by emitting laser beams and measuring reflected signals. It is increasingly becoming a key technology to promote the safety, efficiency, and automation level of the rail transit industry. Its application scope is extensive, covering various rail transit forms such as high-speed railways, subways, light rails, cloud rails, freight railways, and industrial internal transportation.
I. Train Operation Safety and Monitoring
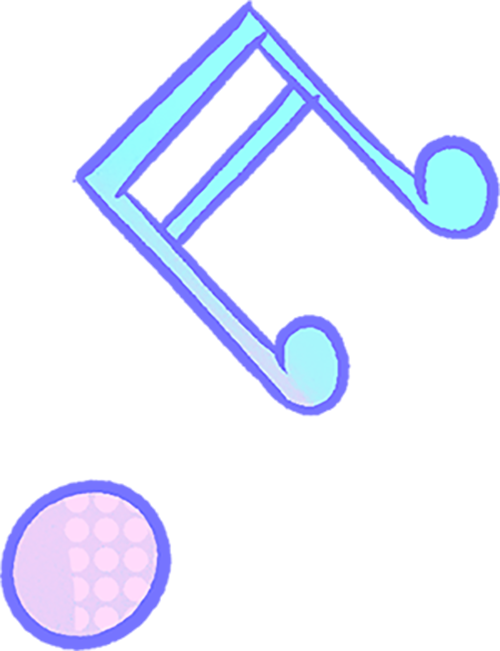
1. Vehicle-end Positioning
When a train enters a tunnel, the GPS signal may be lost. Precise positioning of the train in such environments is crucial for ensuring operational safety. LiDAR can scan the tunnel walls by emitting laser beams like casting a net, and then compare the real-time scanned "point cloud map" with the pre-built tunnel model through algorithms, which can continuously and accurately determine the train's position with an error of less than 5 centimeters! To improve robustness, LiDAR is often tightly coupled with an Inertial Measurement Unit (IMU) to form a LiDAR Inertial Odometry (LIO) to compensate for the degradation problem that LiDAR may encounter in tunnel environments with sparse features or high repeatability (such as long straight and smooth walls). In addition, information such as wheel speed odometry can be fused to further improve positioning accuracy and reliability.
2. Collision Avoidance Warning in Low-speed Scenarios
When trains enter or exit stations, the speed is low, but the environment is complex, and personnel and equipment activities are frequent, making it a high-risk area for accidents. The LiDAR installed at the vehicle end can real-time scan the track and platform edge areas to detect whether personnel, luggage, or other equipment invade the clearance. Once a potential collision risk is found, it can link with the train emergency braking system to effectively prevent low-speed collision accidents.
For scenarios such as scenic spot small trains and cloud rails with relatively open operating environments and possible visual blind spots, LiDAR can also be used to scan areas such as the bottom and sides of the vehicle that are difficult for the driver to cover, timely detect small animals, children, or lost items that may be intruding in,and issue warnings through buzzers and other means.
3. Adaptability to Harsh Environments
Snow-clearing Track Vehicle Operations: In winter snowy areas, track snow or ice seriously affects train operation safety. Snow-clearing track vehicles need to be able to operate in low visibility conditions such as heavy snow and fog. LiDAR, especially models with certain harsh weather penetration capabilities (such as specific wavelengths and multi-echo technology), can penetrate the snow curtain, effectively identify the track boundary and the distribution of snow/ice, and accurately guide the snow-clearing device.
High-temperature and Dust Environments: In industrial scenarios such as steel plants or coal and ore transportation, the rail transit system often faces extreme environments such as high temperature and dust. The LiDAR system (especially those specially designed and protected) can maintain stable operation in these environments, such as being used for positioning and collision avoidance of molten iron tank cars or loading monitoring of bulk freight cars.
II. Track Maintenance: From "Post-event Maintenance" to "Pre-disease Prevention"
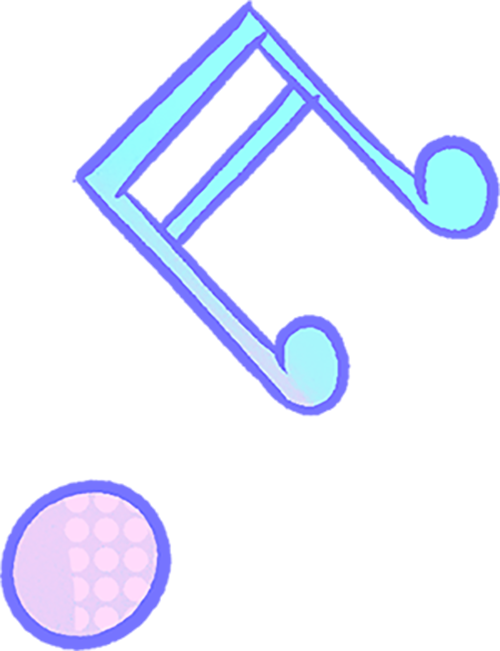
1. Track Inspection and Disease Detection
Unmanned aerial vehicles or inspection vehicles equipped with LiDAR passing through the rail can generate high-density 3D point cloud models. By analyzing the point cloud data, various track diseases can be detected, including track geometric deformation (such as gauge, level, high and low), line settlement, roadbed collapse, ballast loss or hardening, fastener loss or loosening, rail wear, and surface defects (such as scratches, peeling, cracks), etc.
For railway lines built along mountains, fixed or regularly repeated LiDAR scans can be used to long-term monitor potential risk slopes. By comparing point cloud data from different periods and analyzing slope displacement and deformation, geological disasters such as landslides or debris flows can be warned 1-2 hours in advance, striving for precious time to take emergency measures.
High-precision and high-density 3D point cloud data can not only detect obvious faults but also capture millimeter-level early diseases. By registering and comparing LiDAR scan data from different periods, the change process of the geometric state of the track structure can be quantified and analyzed. Based on these time-series data, a track degradation model can be established to predict the occurrence and development trend of diseases. Accordingly, the railway department can scientifically formulate maintenance plans, intervene in advance, improve line safety, reduce maintenance costs, and reduce interference with operations.
2. Catenary-Pantograph System Detection (Overhead Contact System and Pantograph)
The geometric state of the Overhead Contact System (OCS) directly affects the stable current collection of the train. Using the LiDAR system installed on the detection vehicle, the key geometric parameters of the catenary can be measured non-contact and efficiently, including the height of the contact wire (guide height), the offset relative to the track centerline (pull-out value), and the wear degree of the contact wire. At the same time, structural defects on the catenary can also be detected, such as wire strand breaks, cracks, and suspended foreign objects (such as kite strings, bird nests, etc.). The precise 3D shape of the catenary support can also be obtained. By analyzing its verticality (tilt degree), the stability of the support can be evaluated, and problems such as tilting and deformation can be timely discovered to prevent catenary accidents caused by support collapse.
The pantograph is a key component for the train to draw power, and its condition directly affects power supply safety. LiDAR combined with high-speed cameras and other sensors can form a catenary-pantograph comprehensive monitoring system, which is used to monitor the wear of the pantograph slide (remaining thickness), attitude (tilt/yaw), and the contact state of the catenary-pantograph (offline, arcing, etc.); using the precise position of the catenary obtained by LiDAR provides a benchmark for analyzing the dynamic response of the pantograph; some systems use the installation method beside the line to capture and analyze when the train passes.
The LiDAR-based detection vehicle can generate a 3D point cloud model of the catenary. By comparing it with historical data or design benchmarks, the current geometric deviations and defects can be identified, the development trend can be analyzed, and the future state can be predicted; with the help of AI technologies such as deep learning, the automatic recognition rate of catenary components in the point cloud can be improved. An automated system replaces or supplements manual inspection to improve detection efficiency and coverage.
III. Intelligent Stations: Passenger Flow Management
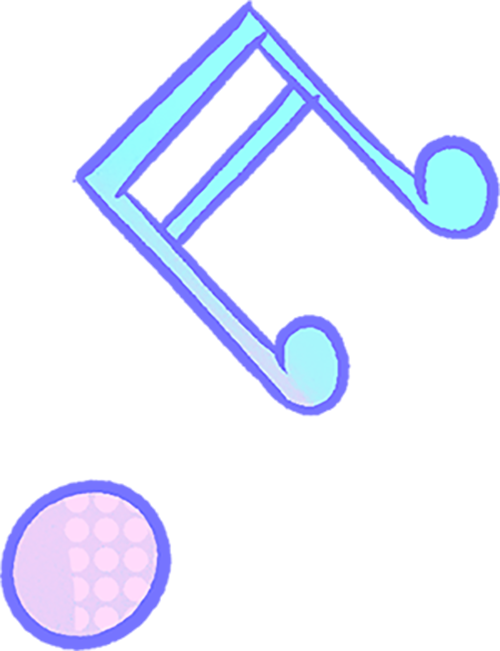
1. Intelligent Security and Operational Optimization
In densely populated areas such as stations, LiDAR scanning key points can real-time and accurately count passenger flow and crowd density and generate a "heat map". The data can be used to optimize train scheduling and dredge passenger flow, and also support business analysis (such as evaluating shop rents and optimizing advertising space settings).
By analyzing the movement locus and posture of pedestrians through 3D point cloud data, and with the help of gait analysis algorithms, abnormal behaviors such as falling and fainting can be quickly identified, and the emergency system can be linked to shorten the response time to within 2 minutes. At the same time, it can also detect situations such as luggage retention, regional congestion, and personnel entrapment and automatically alarm.
2. Asset Protection and Environmental Monitoring
In key areas such as station energy stations and signal rooms, LiDAR can carry out perimeter protection during nighttime or non-operational periods. It can accurately identify moving targets such as personnel, vehicles, and animals. Once illegal intrusion is detected, it will immediately alarm and can also link cameras or drones for tracking and confirmation.
Platform screen doors are related to passenger safety. LiDAR can be installed near the platform doors to real-time scan the area in front of the door and the door gap, real-time monitor whether passengers or items are trapped in the door,or whether someone is trying to cross the platform door to enter the track area under abnormal conditions (such as when the train has not arrived at the station).
IV. Cargo Transportation and Loading Management
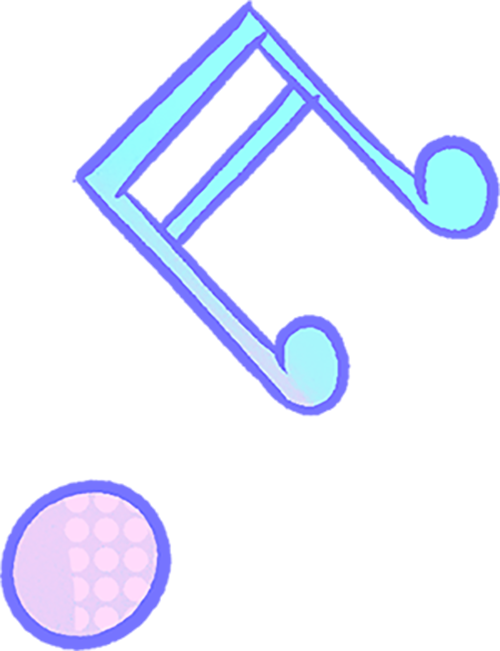
1. Bulk Cargo Transportation Monitoring
After the freight car is fully loaded, LiDAR can quickly generate a 3D model by scanning the cargo surface, and estimate its weight by combining the cargo density with an accuracy of more than 99%! It can also detect whether the cargo's center of gravity is offset beyond the safe threshold, issue a warning, and prompt to adjust the loading or limit the running speed to prevent the vehicle from overturning or derailing. Prevent cargo from spilling during transportation, causing losses and environmental pollution.
2. Container Handling Assistance
In port or railway container yards, LiDAR can quickly scan and generate a 3D model of the entire yard, accurately record the position, number of layers, and attitude of each container (with an accuracy of up to ±2 centimeters), and assist equipment such as cranes in precise container grabbing and placing operations. During port-rail intermodal transportation, it can also track the position of transfer vehicles, optimize scheduling, and shorten the container stay time in the port.
3. Automatic Train Coupling and Uncoupling Assistance
Traditional train coupling and uncoupling rely on manual operation and visual judgment, which is inefficient and has safety risks. Now LiDAR can realize the automation assistance of coupling and uncoupling operations. By scanning the outline of the car end (focusing on the coupler and buffer area), the horizontal/vertical alignment deviation can be real-time and accurately measured; the relative position and attitude of the car can be continuously monitored, and abnormal shaking, deviation, or track micro-deformation can be detected to warn derailment risks. It provides precise guidance for the automatic coupling and uncoupling robot, plans the trajectory of the mechanical arm to automatically complete the connection, and can also scan to confirm the locking state, which is safe and efficient.
V. Industrial Rail Transit Applications
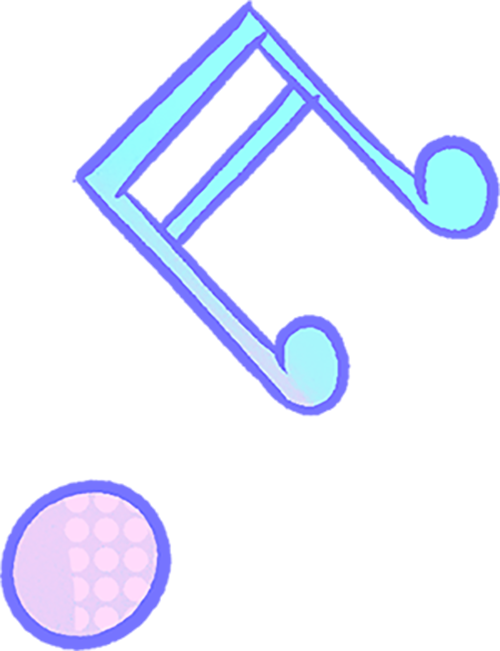
1. Safety Monitoring and Risk Warning within Steel Plants
In steel plants, tank cars transporting high-temperature molten iron are major hazard sources. Through LiDAR scanning, the dynamic monitoring of the tank's tilt angle and internal molten iron liquid level (combined with algorithms) is realized to prevent molten iron from overflowing/tank car overturning due to excessive tilting or shaking, and the real-time positioning, trajectory tracking, and collision avoidance warning of the tank car can also be completed.
2. Safety Guarantee for the Operation of Rail-mounted Trolleys
Real-time scan of obstacles such as scattered scrap steel and slag on the track to avoid trolley derailment; in dusty and extreme temperature scenarios, continuously scan the trolley loading to identify illegal conditions such as center of gravity offset, overloading, and cargo size exceeding the limit, optimize the loading method, reduce uneven track wear, and reduce energy consumption. At the same time, check the carriage height,tarpaulin damage, illegal climbers, or hanging foreign objects, etc., to realize the full-process control of loading and transportation safety.
LiDAR is reconstructing the safety and efficiency of rail transit with "3D vision". In the future, with technological upgrades, we may see more scenarios of "driverless trains" and "fully automatic intelligent stations" - and LiDAR is the key to opening the era of intelligent transportation.